What are the key distinctions between a conventional lathe and a Computer Numerical Control (CNC) lathe?
Release time:
Mar 11,2025
Different Definitions
In simple terms, a CNC lathe is a machine tool that is controlled by numbers. It is an automated machine tool with program automation control. The entire system can logically process control codes or other symbol instructions specified by the program, then automatically compile them, and conduct comprehensive compilation to ensure that the movements of the entire machine tool can be carried out according to the original program for processing.
The control unit of this type of CNC lathe handles all the operations and monitoring of the CNC lathe. It is equivalent to the brain of a device. The equipment we usually refer to mainly refers to the machining center of the CNC lathe.
A conventional lathe is a horizontal lathe that can process various types of workpieces such as shafts, discs, and rings through multiple processes. It is commonly used for processing the internal and external rotary surfaces, end faces, and various internal and external threads of workpieces. With the corresponding tools and accessories, it can also perform drilling, reaming, tapping, and embossing.
Different scopes
The CNC lathe is not merely equipped with one CNC system; it also incorporates numerous different technologies. It is precisely through the utilization of various technologies that it encompasses a wide range of applications.
This includes CNC lathes, CNC milling machines, CNC machining centers, and CNC wire-cutting machines, among other different types. Such a technology involves the conversion of digital program language symbols and then processing the entire computer-controlled machine tool.
Different advantages
Compared to processing products with ordinary machine tools, using a CNC lathe for processing products has many advantages. When processing products with a CNC lathe, production efficiency can be significantly enhanced. After the entire workpiece is clamped, the already compiled processing program is input.
The entire machine tool can then automatically complete the processing process. Generally speaking, when the parts to be processed change, only a series of CNC programs need to be modified. Therefore, to a certain extent, this can significantly shorten the entire processing time. Compared to processing with machine tools, it can achieve the highest production efficiency.
CNC lathes are one of the widely used CNC machine tools at present. They are mainly used for the cutting processing of the inner and outer cylindrical surfaces of shaft parts or disc parts, the inner and outer conical surfaces with arbitrary cone angles, complex rotary surfaces with curves, cylindrical and conical threads, etc., and can also perform slotting, drilling, reaming, tapping and boring.
A CNC machine tool processes the workpiece automatically in accordance with the pre-prepared processing program. We compile the processing technology route, process parameters, the motion trajectory of the cutting tool, displacement amount, cutting parameters and auxiliary functions of the workpiece into a processing program list according to the instruction codes and program formats prescribed by the CNC machine tool. Then we record the contents of this program list on the control medium and input it into the CNC device of the CNC machine tool, thereby commanding the machine tool to process the workpiece.
- The processing accuracy is high and the processing quality is stable.
- It can achieve multi-coordinate linkage and is capable of processing parts with complex shapes.
- When the processing parts are changed, generally only the NC program needs to be modified, which can save the time for production preparation.
- The machine tool itself has high precision and great rigidity. Therefore, it is possible to select the appropriate machining allowance, resulting in high productivity (generally 3 to 5 times that of ordinary machine tools).
- The machine tool is highly automated, which can reduce the labor intensity.
- The requirements for the operational skills of the personnel are quite high, and the technical standards for the maintenance personnel are even higher.
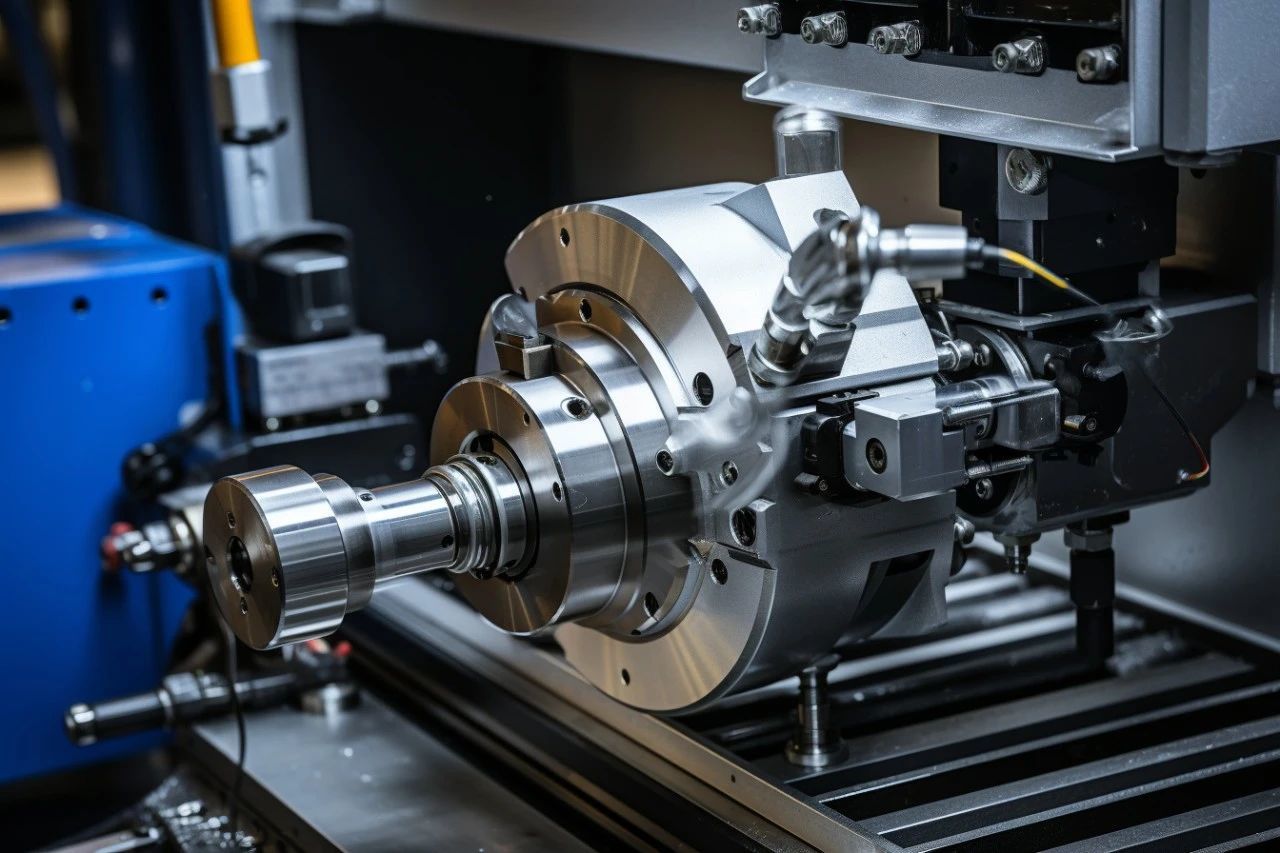
To determine the processing requirements of typical parts and the batch size of the workpieces to be machined, and to formulate the functions that a CNC lathe should possess as the prerequisite for making proper preparations and selecting a CNC lathe reasonably: these are all based on meeting the processing requirements of typical parts.
The main technical requirements for typical parts are the structural dimensions, processing range and precision requirements of the parts. According to the precision requirements, that is, the size precision, positioning precision and surface roughness requirements of the workpiece, the control precision of the CNC lathe is selected. Based on reliability, reliability is the guarantee for improving product quality and production efficiency. The reliability of CNC machine tools refers to the fact that the machine tool can perform its functions stably and without faults for a long time under specified conditions. That is, the average time without faults is long. Even if a fault occurs, it can be restored within a short period of time and put back into use. Choose machine tools with reasonable structure, excellent manufacturing quality, and mass production. Generally, the more users there are, the higher the reliability of the CNC system.