Basic knowledge of vertical machining center
Release time:
Feb 11,2025
WUXI RUIEN to provide you with one-stop machining center services, we have a range of machining centers including 3, 4, 5 axis machine tools, fully capable to meet your processing projects.
Vertical machining center is an indispensable part of the development of modern numerical control technology. CNC vertical machining centers can process parts from different industries, these machines are versatile and efficient. This article will discuss vertical machining centers, their working principles, components, applications, and factors to consider when choosing the right machining center for your project.
What is a vertical machining center?
Vertical machining centers are one of the most productive tools on the shop floor, and their tool changer and other devices increase productivity. At the same time, it is a flexible and versatile tool, running in the vertical direction using a spindle that works at multiple angles.
Computer control of the vertical milling machine enables automation, tool selection/rotation, repeatable machining, and profile control. These modern numerical control technologies have brought the productivity of machine tools to a high level, resulting in automated vertical milling centers and turning centers.
Vertical machining centers can be said to be the main force of the industry, as it can process parts with higher accuracy and shorter lead times. Its components are designed to be robust and provide excellent torque, horsepower and processing speed. The degree of automation of vertical machining centers also enables them to cut various materials and reduce the overall manufacturing cost.
Working principle of vertical machining center
Vertical machining centers operate according to the cooperation of internal components, and the parameters required by the machine tool and processing are converted into information codes, which can usually be accepted and read by the numerical control device of the machine tool.
The processing program can automatically process the program of the component, and the instruction code is usually stored on the information carrier such as disk, and the carrier is sent to the input device, which can read the information and transmit it to the numerical control device. In addition, the computer can also be used to directly send information to the processing center, to achieve the input and output of the program.
The vertical machining center generally has three linear motion coordinates, and its workbench is also connected with a horizontal axis rotating workbench, which helps it easily process various shapes of the workpiece.
Components of vertical machining centers
A vertical machining center consists of many components, which include the following:
Spindle of rotation
The spindle, usually perpendicular to the table, is a rotating shaft with a device for holding the tool in place. Generally speaking, the spindle plays the role of positioning, supporting and rotating drive.
Standard work table
The table is flat and the workpiece can be placed on it directly or using a fixture. The X-axis of the table includes left and right movement, and the Y-axis includes front and rear movement. With these axes and the Z-axis, you can add machining features to the workpiece across the entire motion plane.
Tool changing device
The tool changer automatically selects the tool for different tasks from roughing to finishing, thereby increasing the productivity of the vertical machining center.
Rotary working table
Adding additional axes to a vertical milling machine can transform a simple three-axis milling machine into a four-or five-axis machine, resulting in a significant increase in productivity for machining complex parts with different surfaces.
Cooling system
Most CNC vertical milling centers use efficient cooling systems to ensure that the parts and tools are well lubricated. Such cooling systems typically use a variety of liquids such as water and soluble oils.
Protective cover
These shields help reduce splashes from processing operations. Similarly, it protects mechanics and the environment from processing operations.
Fast loader
The fast part loading system helps to increase the productivity of CNC vertical machining centers while reducing downtime.
Chip conveyor
Chip conveyors can help move chips away from the work area, thereby increasing productivity and reducing downtime for manual removal of waste chips.
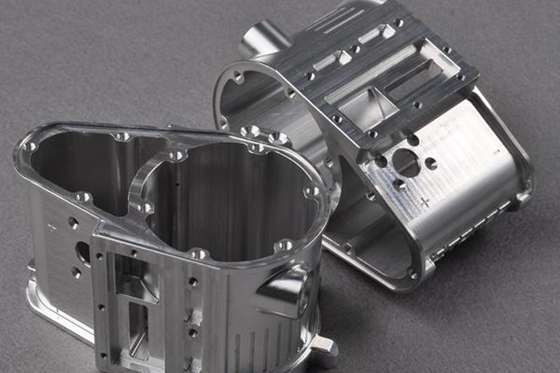
Application of vertical machining center
CNC vertical machining centers can process a variety of parts and products for different industries. Industries such as aerospace, automotive industry, mechanical equipment, and medical are using this CNC machining technology due to its high precision, high accuracy, and mass production.
Here are some of the types of parts that vertical machining centers can process:
A part of irregular shape
Structures such as brackets or bases have irregular shapes, and most of these parts require multi-point hybrid processing of points, lines, and faces, while vertical machining centers with automatic processing capabilities can process these parts with complex shapes.
Box type parts
A box part is a part with a hole system and multiple internal cavities. These box-type parts are common in automobiles and aircraft, such as engine blocks, headstock, gear pump housing, etc. Using the vertical machining center, a clamping can complete the operation of the ordinary machine tool 60-95%.
In addition, the vertical machining center also has high precision, high efficiency, high rigidity and automatic tool change function, as long as the program design is reasonable, the fixture and tool use is proper, can be efficient processing box parts.
Parts with complex curves
Components such as propellers, cams, and impellers have complex curves and are common in the aviation and transportation industry. It is difficult for traditional machine tools to process parts with curved surface, high surface profile and closed inner cavity, and it is difficult to achieve ideal machining accuracy.
However, multi-axis vertical machining centers combined with CNC technology can efficiently process complex curved parts with these characteristics in a shorter time.
Trial production of new parts
Vertical machining centers are highly flexible and adaptable. When you need to change a processed object, you can create and enter new programs, change certain program segments, or use special instructions.
For example, you can use the scaling function to produce parts of the same shape but different dimensions. This provides great convenience for small batch production, trial production of new products or production of multiple varieties. In addition, it can shorten the production preparation and trial production cycle.
WUXI RUIEN to provide you with one-stop machining center services, we have a range of machining centers including 3, 4, 5 axis machine tools, fully capable to meet your processing projects.