CNC Machining Centers Explained: 3-Axis vs. 4-Axis vs. 5-Axis
Release time:
Feb 28,2025
The machining center is a CNC machine tool equipped with a tool library, with automatic tool change function, and carries out multi-process processing after one clamping of the workpiece. Machining center is highly mechatronics products, workpiece clamping, CNC system can control the machine tool according to different processes automatically select, replace the tool, automatic tool, automatic change the spindle speed, feed, etc., can continuously complete drilling, boring, milling, reaming, tapping and other processes. Therefore, the workpiece clamping time, measurement and machine tool adjustment and other auxiliary process time are greatly reduced, and the processing shape is more complex, the precision is higher, and the parts with frequent variety replacement have good economic results. So, what is the specific difference between the three-axis, four-axis and five-axis machining centers that we often say?
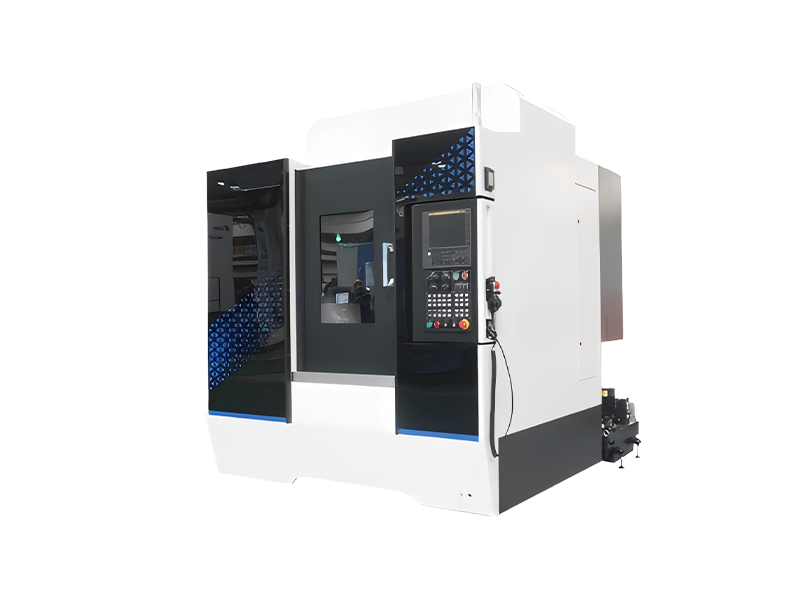
One, three axis machining center
Three-axis CNC milling is still one of the most popular and widely used machining processes. The three-axis vertical CNC machining center is a linear movement of three axes in different directions, respectively up and down, left and right and before and after, the direction of the upper and lower is the main shaft, which can be rotated at high speed. In three-axis machining, the workpiece remains fixed and the rotary tool cuts along the X, Y, and Z axes. This is a relatively simple form of CNC machining that can manufacture products with simple structures and is not suitable for machining complex geometry or products with complex components.
Because it can only be cut on three axes, the machining speed may also be slower than a four - or five-axis CNC, and the workpiece may need to be manually repositioned to obtain the desired shape.
Two, four axis machining center
The four-axis vertical machining center is to add a rotating axis on the basis of three axes, that is, the horizontal plane can be rotated 360 degrees, and can not be rotated at high speed.
In four-axis CNC milling, the fourth axis is added to the motion of the cutting tool, allowing rotation around the X-axis. There are now four axes - the X axis, the Y axis, the Z axis and the A axis (rotating about the X axis). Most four-axis CNC machines also allow the workpiece to rotate, the so-called B-axis, so that the machine can act as both a milling machine and a lathe.
If you need to drill into the side of a part or the curved surface of a cylinder, four-axis CNC machining is the way to go. It greatly speeds up the processing process and has high machining accuracy.
Three, five axis machining center
The five-axis machining center has one more axis that can rotate 360 degrees upright than the four-axis machining center, and can not rotate at high speed. The rotation axis is usually above the upper and lower axis, that is, above the main axis, and the fifth axis is rotating around the Y axis, also known as the B-axis. The workpiece can also be rotated on some machines, sometimes referred to as the B-axis or C-axis. The five-axis machining center can process parts such as statues, impeller blades and integral leaf discs at one time, and can also use shorter tools for processing, improving the rigidity of the system, reducing the number of tools, and avoiding the production of special tools. For our business owners, it means that in terms of tool costs, five-axis machine tools will save money
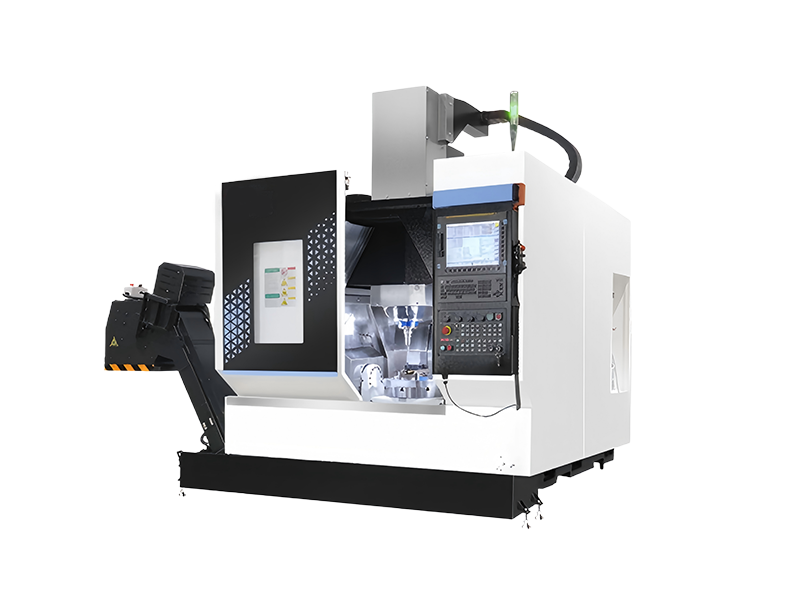
The five-axis machining center has two rotation modes.
Table rotating shaft, the workpiece can be divided into any Angle processing, processing inclined plane and inclined hole, choose high-end CNC five-axis system and software RETP support, can also process complex spatial surfaces, this type of five-axis machining center advantage is the spindle structure is simple, rigid or, the disadvantage is that the bearing is relatively small.
The main shaft swinging head rotation, the front end of the main shaft is the rotary head design, the advantage is that the processing of the main shaft can be very flexible, the table can carry more weight, when the use of spherical milling surface machining surface, the tool center line and the vertical face of the processing surface can effectively avoid the apex cutting, can ensure the linear speed, but also improve the surface processing quality, The mold surface requires higher precision and chooses this structure more. In order to achieve more precise rotation accuracy requirements, it can also be equipped with a grating ruler. Accuracy can reach a few seconds, but the price is slightly higher.