Comprehensive Analysis of Surface Grinding Machine Components: Functions and Features Explained
Release time:
Feb 18,2025
Surface grinding machine is a kind of precision machining equipment, the coordinated operation of its various parts is very important for the final machining accuracy.
Surface grinding machine is a kind of precision machining equipment, the coordinated operation of its various parts is very important for the final machining accuracy. This paper will analyze the main components of the surface grinder in detail, deeply discuss their respective functions and roles, and combined with practical application scenarios to explain, to help readers better understand and operate the surface grinder.
First, the bed
1, the bed is the basic part of the surface grinder, it is as important as the foundation of the house. It supports the various components of the grinder and withstands various forces and vibrations during processing. The bed is usually made of high-strength cast iron material to ensure its stability and rigidity.
2, the structure of the bed is diverse, the common closed bed and open bed. Closed bed with high rigidity and stability, suitable for heavy cutting; The open bed is easier to operate and maintain.
3, the accuracy of the bed guide directly affects the machining accuracy of the grinding machine. Therefore, the manufacture and maintenance of the bed rail are very important. The common guide rail forms are V-shaped guide rail, flat V guide rail and dovetail guide rail.
Two, workbench
1, the workbench is used to install and clamp the workpiece parts. It can move vertically and horizontally on the bed to achieve the feed movement of the workpiece. The moving accuracy and stability of the table directly affect the grinding quality.
2, the driving mode of the workbench is usually mechanical transmission, hydraulic transmission and CNC servo transmission. CNC servo drive has higher accuracy and efficiency, and can realize automatic processing.
3. The surface of the workbench is usually equipped with a T-shaped slot for installing various fixtures and workpieces.
Three, grinding head
1. The grinding head is the core component of the surface grinder, which includes the grinding wheel and the drive motor. The grinding head can be moved in a vertical direction to adjust the grinding depth.
2. The spindle of the grinding head rotates at high speed to drive the grinding wheel. The precision and stability of the spindle are crucial to the grinding quality.
3, the feed mechanism of the grinding head can control the grinding depth and feed speed. Common feed methods include manual feed, automatic feed and numerical control feed.
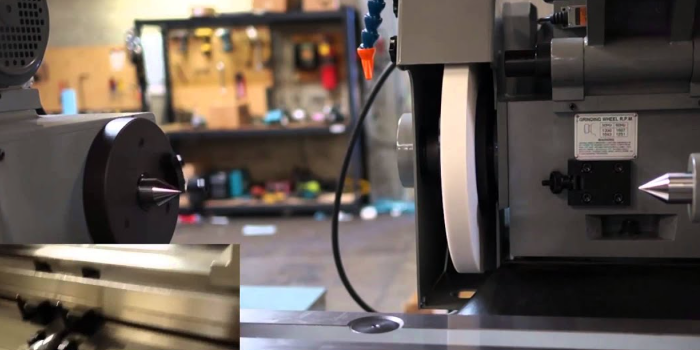
Four, grinding wheel
1, the grinding wheel is the cutting tool of the surface grinder, which is composed of abrasive, binder and other additives. The choice of grinding wheel should be considered according to the factors such as the material to be processed, the grinding method and the accuracy requirements.
2. The granularity, hardness and organization of the grinding wheel are important parameters of the grinding wheel. The particle size indicates the size of the abrasive particles, the hardness indicates the strength of the binder, and the organization indicates the distribution density of the abrasive particles.
3, the balance of the grinding wheel is very important, the unbalanced grinding wheel will cause vibration, affect the grinding quality, and even damage the machine tool.
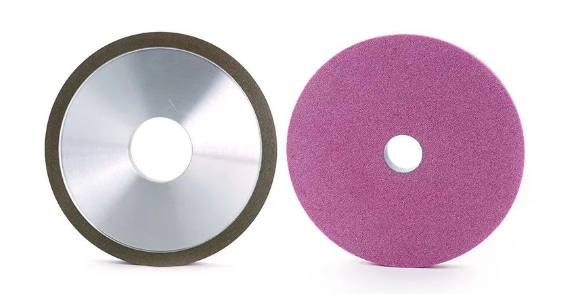
Five, cooling system
1, the role of the cooling system is to reduce the temperature in the grinding process, reduce the wear of the workpiece and the grinding wheel, and improve the grinding efficiency and quality.
2, the common cooling methods are water-cooled and oil-cooled. The cooling effect of water cooling is better, but it is easy to cause workpiece rust; Oil cooling is not as effective as water cooling, but it can play a lubricating role.
3. The cleanliness and concentration of the coolant should be checked and maintained regularly.
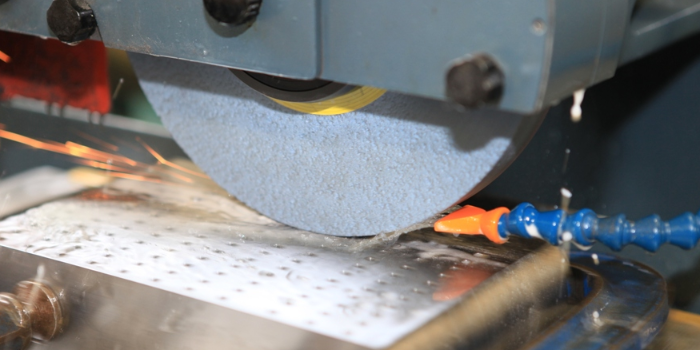
Previous